Don’t know what Total Quality Management (TQM) is? Don’t worry, you are not alone. Despite its great impact on businesses, Total Quality Management remains a concept that many are unfamiliar with.Â
However, what if I tell you that understanding Total Quality Management can unlock the secrets to transforming your organization’s performance and customer satisfaction levels?
In this article, we will be getting insights into Total Quality Management (TQM), its advantages, and its uses.
Total Quality Management- Key Takeaways
- Understanding what Total Quality Management is.
- Discussing the advantages of Total Quality Management in Businesses.
- Getting insights into the basic principles of Total Quality Management.
What Is Total Quality Management?
Total quality management (TQM) is a continuous process of finding and fixing mistakes in manufacturing. It helps organizations to make the supply chain more efficient, improves customer satisfaction, and ensures that employees receive proper training.Â
The main goal of TQM is to make sure that everyone who is involved in the production process is contributing to the quality of the final product.
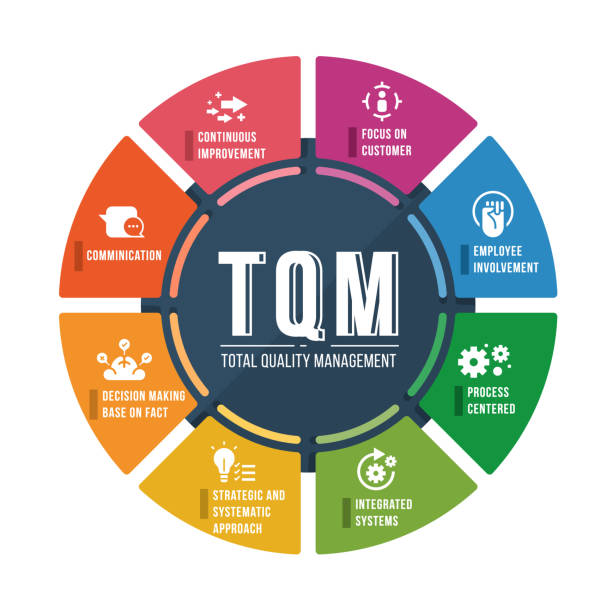
Understanding Total Quality Management (TQM)
Total Quality Management (TQM) is a method used by businesses to manage an organization’s overall quality. Its goal is to improve the quality of products and services by continuously improving internal processes. The standards in TQM can come from both the organization’s needs and the existing industry requirements.
These industry standards can vary and may include following laws and regulations related to the business. They can also involve producing goods or services that meet common expectations, even if not officially required by law.
Principles Of Total Quality Management (TQM)
Total Quality Management(TQM) uses some techniques, methods, and strategies to enhance the quality and customer satisfaction in the organization. Some basic principles of Total Quality Management are-
- Customer-focused: The quality of a product or service is decided by whether customers find it valuable or not. No matter how hard a company tries to improve quality by training staff, designing products better, or updating technology. it’s ultimately the customers who decide if these efforts are worth it or not.
- Total Employee Involvement: All employees work together towards common goals. This happens best when employees feel valued and empowered, and when management creates a supportive environment.Â
- Process-Centered: TQM uses a clear and organized method to improve the overall quality. It focuses on processes like- including flowcharts, prototypes, diagrams, visual plans, and written workflows. Everyone involved in the process needs to know their role and understand what to do at each stage. This helps to make sure that every step is done correctly and timely. These processes are regularly checked and reviewed to find any problems and make improvements.
- Integrated System: Even though organizations have different departments, what’s important in TQM is how these departments work together to create the best version of the product. Small tasks add up to bigger ones, and all these tasks lead to the organization’s overall success. Everyone working in the team should be aware of the organization’s goals, quality policies, and what’s critical for success.
- Strategic and Systematic Approach: Total Quality Management (TQM) believes in systematic and strategic planning to achieve the organization’s goals and mission. They mainly plan things in a step-by-step manner which is easy to understand and work upon.
- Continual Improvement: TQM is all about always getting better. It pushes organizations to think smart and find new ways to be more competitive and meet stakeholder needs better. This idea of continuous improvement helps the company to stay flexible and adapt to changes in the market. It also makes the business more suited to different products, markets, customers, or regions.
- Fact-Based Decision Making: To know how well a company is doing, it needs data. Total Quality Management (TQM) says organizations should always gather and study data to make better decisions and predict future outcomes based on past experiences.
- Communications: Good communication is key, especially during daily work. It keeps morale high and motivates employees. It’s not just about what is said, but how and when it’s said.
Benefits Of Total Quality Management
Implementing a Quality Management System in the organization benefits an organization in almost every aspect. Below are some most important benefits of Total Quality management that help an organization to grow.
- Improved Customer Satisfaction: TQM helps businesses to make products and services that customers love to buy and use. This leads to increased customer satisfaction and more business growth.
- Higher Quality Products: By focusing on quality at every step, TQM helps companies to create better versions of products that meet customer needs and expectations. This will help your business to stay competitive in the market by creating greater brand value.
- Increased Efficiency: Total Quality Management (TQM) helps businesses to streamline their overall process. By making operations more efficient and cost-effective; you can manage your time, money, resources of a company in a more efficient way.
- Stronger Competitive Edge: With improved quality, efficiency, and customer satisfaction; companies using total quality management (TQM) can overpower competitors and become a stand out choice in the market.
- Continuous Improvement: Total Quality Management (TQM) encourages regular learning and improvement, this ensures that businesses stay relevant to the new technology and adapt to changing needs and trends regularly.
Implementing Total Quality Management
Before setting up a Total quality management system, your organization needs to identify different connected processes that help in keeping customers happy. The design of the Total Quality Management System mainly depends upon the organization’s goals, needs, and the products or services it offers.Â
This structure is mainly based on a cycle called PDCA (Plan, Do, Check, Act), which allows for continuous improvement in both the product and the QMS. The basic steps to implementing total quality management system are:
- Plan: Plan about how the Quality Management System will work and what it needs to achieve.
- Do: Start creating your Quality Management System based on your plan and objective.
- Check: Make sure the Quality Management System is working as intended and check for any issues.
- Act: Take corrective actions if needed to keep the Quality Management System running smoothly.
- Review: Regularly review the QMS to see if any improvements can be made.
- Improve: Make changes and improvements to the QMS based on your reviews to make it even better.
Industries Using TQM
TQM, or Total Quality Management was initially started in the manufacturing sector but can be used in many different industries. It focuses on long-term improvements rather than fixing things quickly for temporary purposes.Â
Nowadays, Industries like manufacturing, banking, finance, and healthcare use Total Quality Management (TQM) to create necessary changes that can lead to more business growth.
TQM can be applied to all parts of a company. This ensures that everyone is working hard toward the same goals and improving how each area works. It can be used in departments like administration, marketing, production, and employee training to help the company run more smoothly.
Learn Product Management with PW Skills
Are you excited about launching your career as a Project Manager in a top multinational company? If so, PW Skills is your ultimate destination, offering a comprehensive Product Management Course.Â
Enrolling in this course will equip you with all the relevant in-demand skills. You’ll work on capstone projects with expert industrialists. But that’s not all this course will also prepare you for project management interviews and provide you with 100% job assistance, ensuring you step confidently into the relevant field. Ready to kick-start your journey towards success? Join us at PW Skills today!
Total Quality Management FAQs
Why is Total Quality Management(TQM) important?
Total quality management plays an important role in the development of employees and businesses as well, using TQM in businesses leads to increased customer satisfaction, improved efficiency of the company as all the employees are working together, helps companies to have a stronger competitive edge among competitors and much more.
What are the key principles of TQM?
The key principles of TQM include customer focus, continuous improvement, employee involvement, process-centered thinking, data-driven decision-making, and a commitment to quality. You can refer to the above article for a detailed explanation of these principles.
How can organizations measure the success of TQM initiatives?
Organizations can measure the success of TQM by tracking key performance indicators (KPIs) related to quality, customer satisfaction, employee engagement, productivity, cost savings, and Regular reviews or feedback mechanisms also help in measuring the impact of TQM.